Digital Bamboo
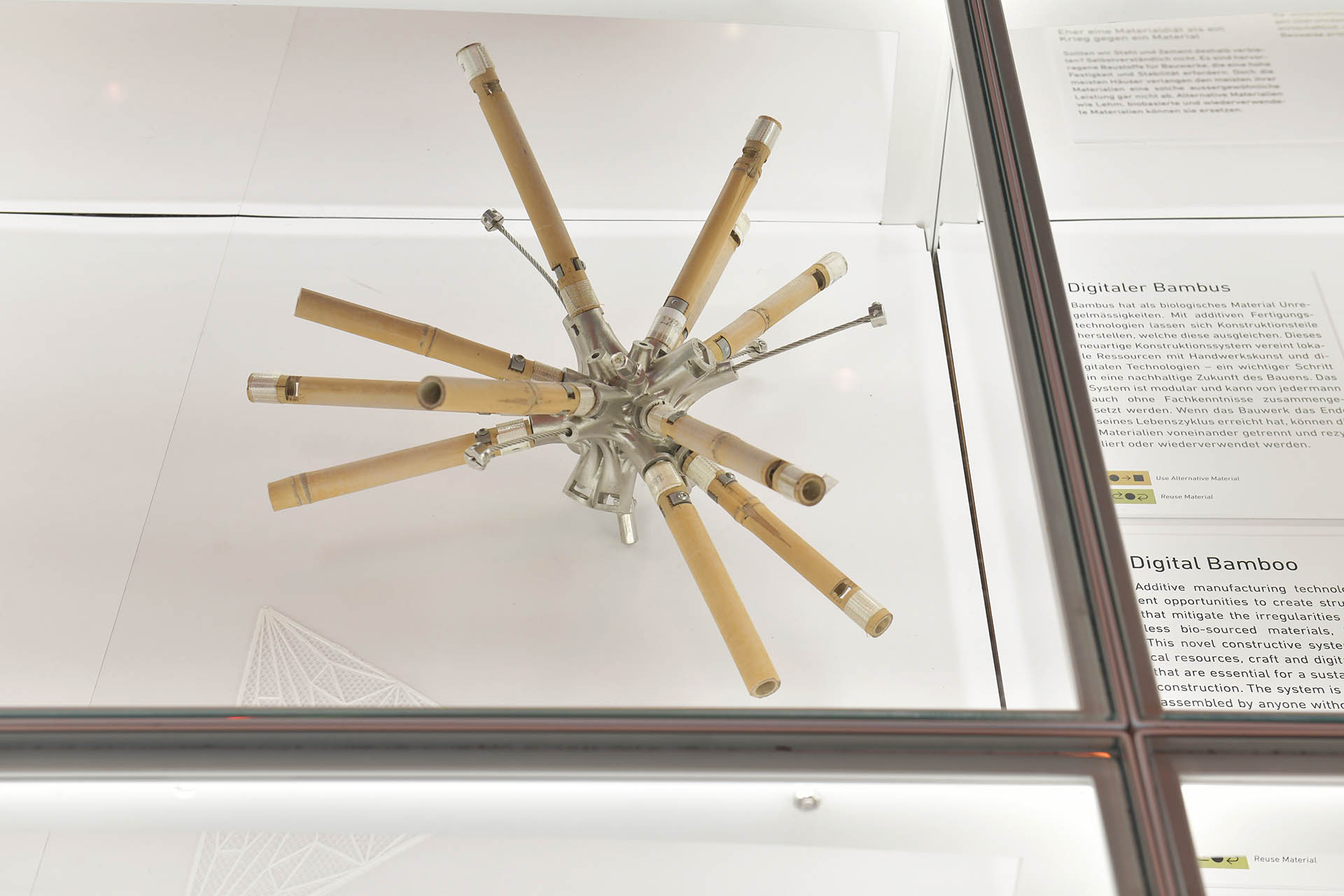
Additive manufacturing technologies present opportunities to create structural parts that mitigate the irregularities of standardless bio-sourced materials, like bamboo. This novel constructive system embeds local resources, craft and digital technologies that are essential for the sustainable future of construction. The system is modular, can be assembled by anyone without any expertise, and can be disassembled entirely at the end of its life so that materials can be separated and recycled or reused.
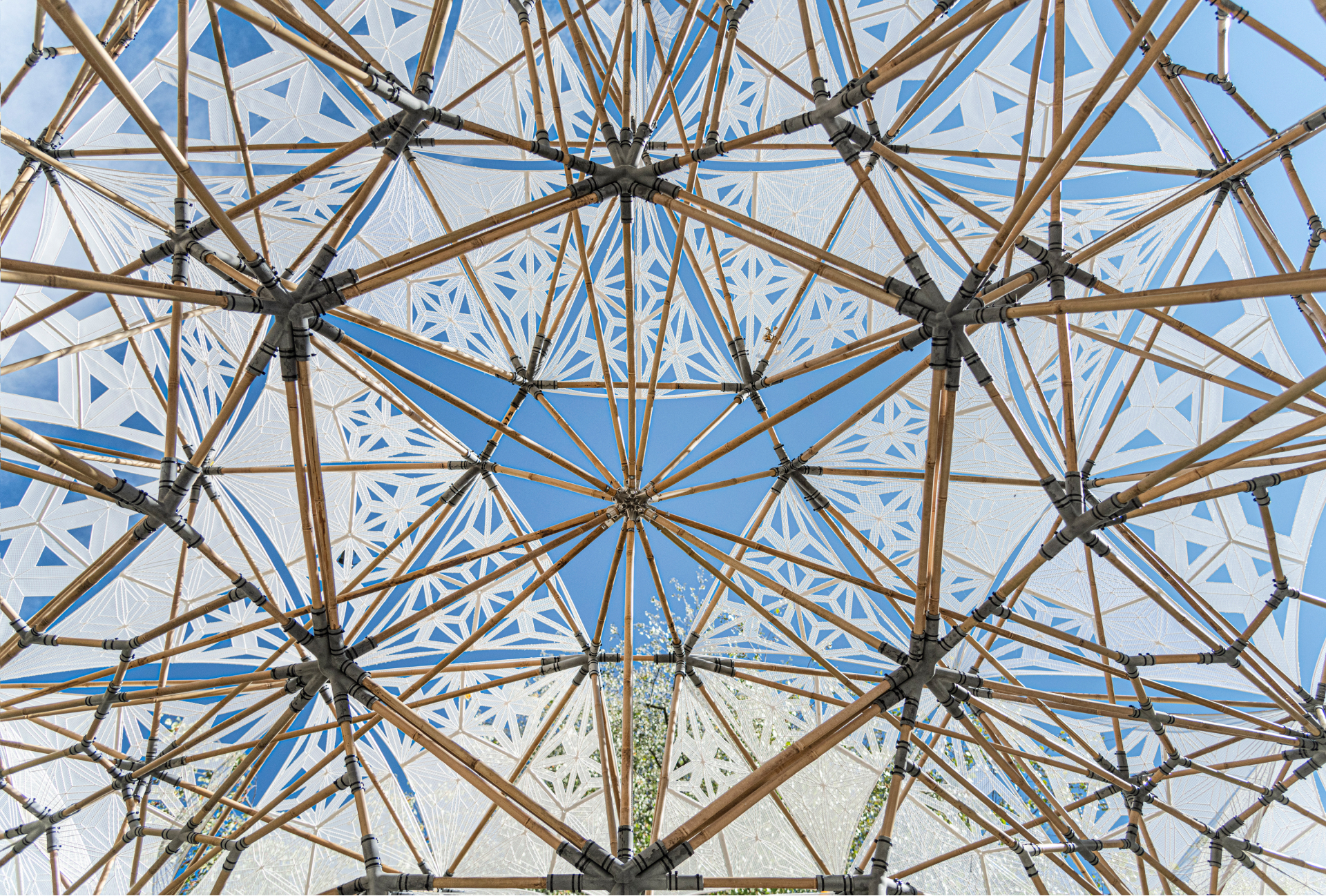
These prototypes envision new constructive systems that leverage the freedom of additive manufacturing technologies. The construction industry is a massive contributor to the global carbon emissions, therefore, it is a pressing challenge to develop sustainable ways to build as the demands for housing and infrastructure increase. Most of the future construction needs will be in the global south, where bamboo grows naturally and is part of local craft and building culture. Developing new constructive systems that embed local resources, craft and digital technologies are essential for a sustainable future of construction.
Bamboo is a fast-growing natural material with a short harvesting cycle that can sequester carbon dioxide throughout its life cycle. Its tubular shape makes it an excellent candidate for replacing energy-intensive metals in space frame construction, where loads are mainly transferred axially. However, the natural variability of unprocessed bamboo poles hinders their use with existing connection systems. This inherent variability can be easily embedded in connection systems that are manufactured with 3D printing technologies in a simple supply chain.
The two different connecting systems were used to fabricate a 40m² prototypical ultralight pavilion. The connections embed multiple functionalities, namely the connection to the lightweight shading panels that were 3D printed by depositing thin layers of rib structures on a porous textile, the post-tensioning cables, bundling of multiple bamboo poles, as well as logistic information for easy assembly. The research on 3D printed bespoke connections is developed at Digital Building Technologies, ETH Zürich. The presented study was applied in the “Digital bamboo” pavilion and exhibited in the ZAZ Bellerive Zurich and the Venice Architecture Biennale 2021.
Visit the project virtually here:
See the different technologies that enabled the development of this project:
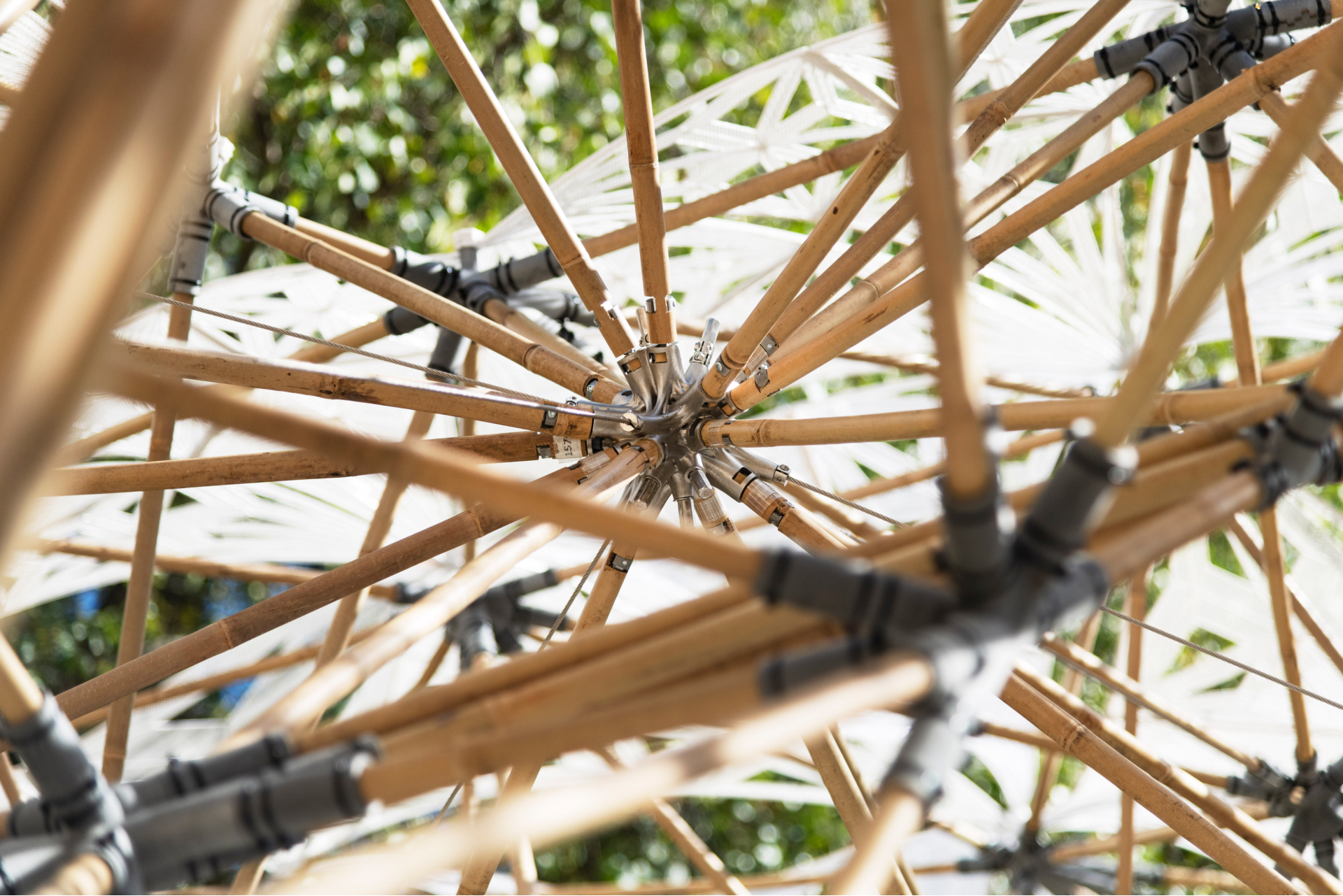
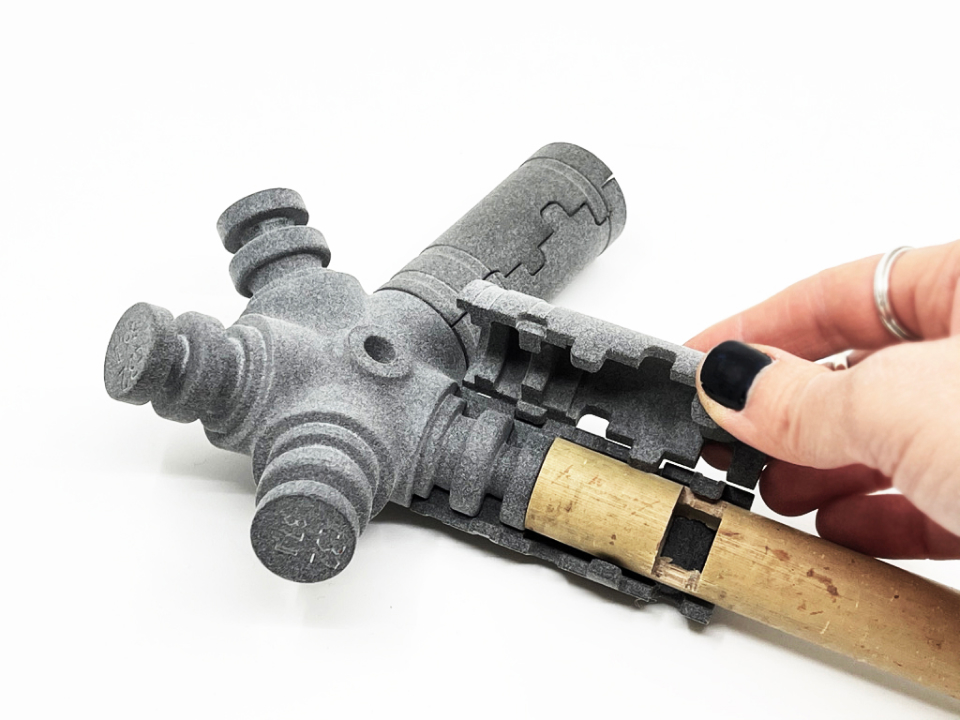