Digitaler Bambus
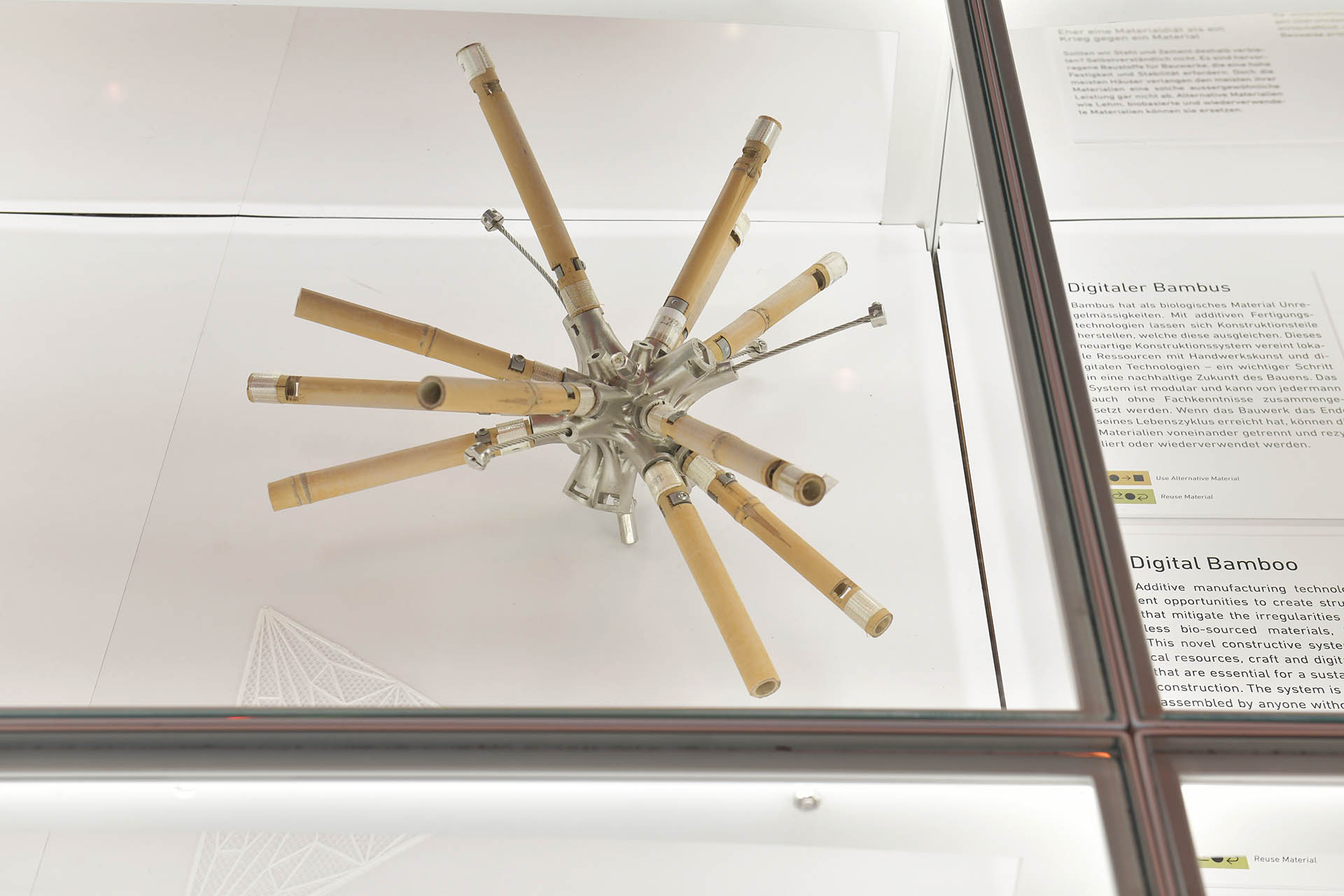
Bambus hat als biologisches Material Unregelmässigkeiten und ist somit nicht genormt. Mit additiven Fertigungstechnologien lassen sich Konstruktionsteile herstellen, welche diese Unregelmässigkeiten ausgleichen. Dieses neuartige Konstruktionssystem vereint lokale Ressourcen mit Handwerkskunst und digitalen Technologien – ein wichtiger Schritt in eine nachhaltige Zukunft des Bauens. Das System ist modular und kann von jedermann auch ohne Fachkenntnisse zusammengesetzt werden. Wenn das Bauwerk das Ende seines Lebenszyklus erreicht hat, können die Materialien voneinander getrennt und rezykliert oder wiederverwendet werden.
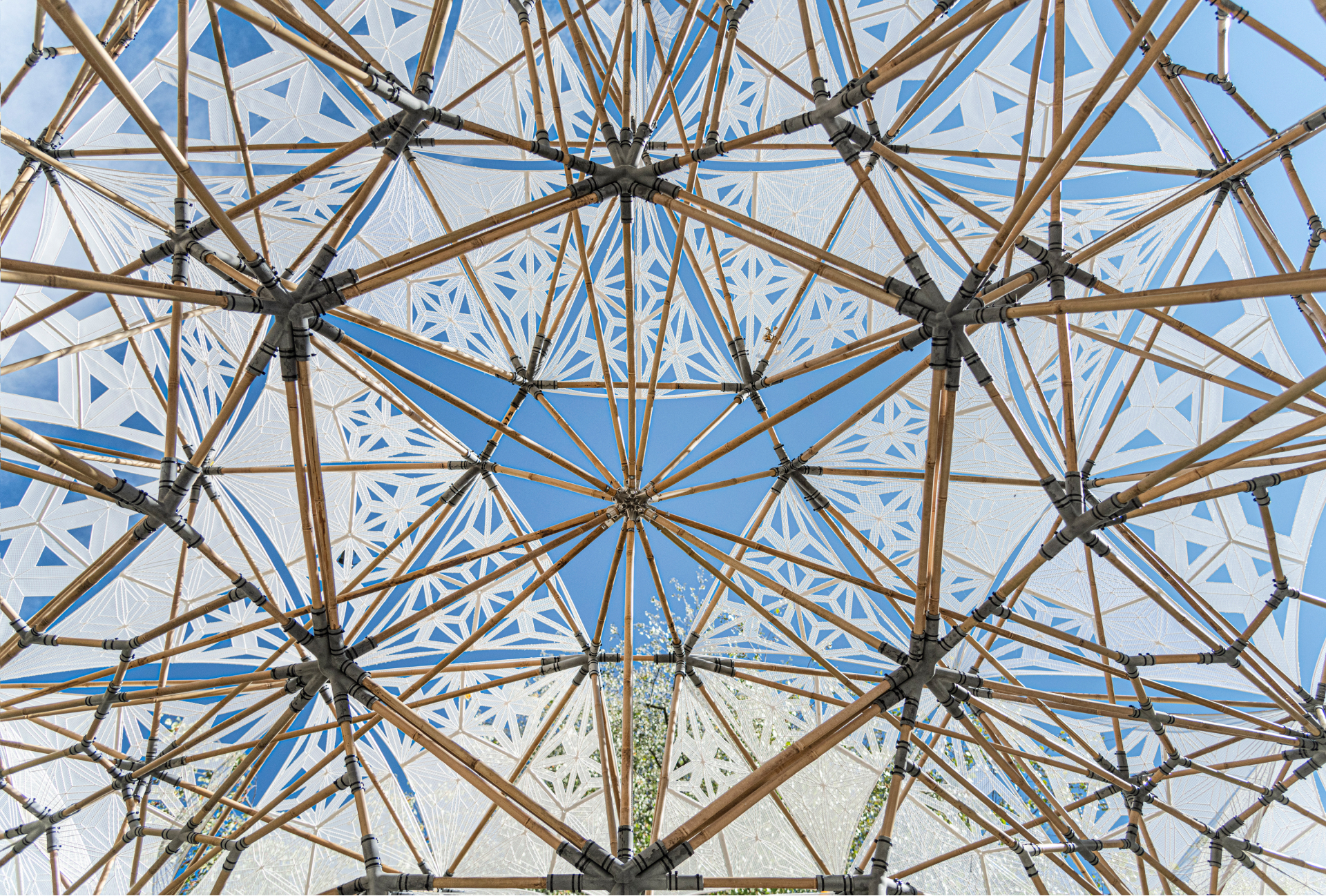
Solche Prototypen veranschaulichen neue Konstruktionssysteme, welche die Freiheiten, die additive Fertigungstechnologien uns bieten, voll und ganz ausschöpfen. Die Bauwirtschaft verursacht einen erheblichen Teil der weltweiten CO₂-Emissionen. Angesichts des zunehmenden Bedarfs an Wohnungen und Infrastruktureinrichtungen ist es deshalb dringend erforderlich, nachhaltige Bauweisen zu entwickeln. Der Grossteil des zukünftigen Baubedarfs wird im globalen Süden liegen. Dort ist der Bambus nicht nur heimisch, sondern auch Teil der lokalen Handwerks- und Bautradition. Die Entwicklung neuer Konstruktionssysteme, die lokale Ressourcen mit Handwerkskunst und digitalen Technologien verbinden, ist ein unerlässlicher Schritt, um die Zukunft des Bauens nachhaltig zu machen.
Bambus ist ein schnell wachsendes, natürliches Material mit einem kurzen Erntezyklus, das während seiner Lebensdauer Kohlendioxid binden kann. Durch seine Röhrenform ist Bambus exzellent geeignet, um in Raumtragwerken, auf die vor allem axiale Lasten wirken, energieintensive Metalle zu ersetzen. Jedoch stehen die natürlichen Unregelmässigkeiten von unbearbeiteten Bambusstäben ihrer Verwendung mit den bislang verfügbaren Verbindungssystemen im Weg. Diese immanenten Unregelmässigkeiten lassen sich jedoch in Verbindungssystemen, die mittels 3D-Drucktechnologie in einer simplen Lieferkette gefertigt werden, leicht berücksichtigen.
Zur Herstellung eines 40 m² grossen Prototyps eines ultraleichten Pavillons wurden zwei unterschiedliche Arten von Verbindungsknoten genutzt. Sie verbinden die im 3D-Druck-Verfahren hergestellten, leichten Verschattungspaneele. Diese wurden in 3D gedruckt, indem dünne Schichten von Rippenstrukturen auf ein poröses Textil aufgebracht wurden. Sie verbinden zudem die Vorspannseile und bündeln die Bambusstäbe; liefern aber auch logistische Informationen für eine einfache Montage. Die Forschung zu den im 3D-Druck hergestellten, massgeschneiderten Knotenpunkten erfolgte am Lehrstuhl für Digital Building Technologies, ETH Zürich. Die vorgestellte Studie wurde im Pavillon «Digital Bamboo» umgesetzt und am ZAZ Bellerive Zürich sowie auf der Architekturbiennale 2021 in Venedig ausgestellt.
Sehen Sie sich das Projekt virtuell hier an:
Erfahren Sie, welche unterschiedlichen Technologien die Entwicklung dieses Projekts möglich gemacht haben:
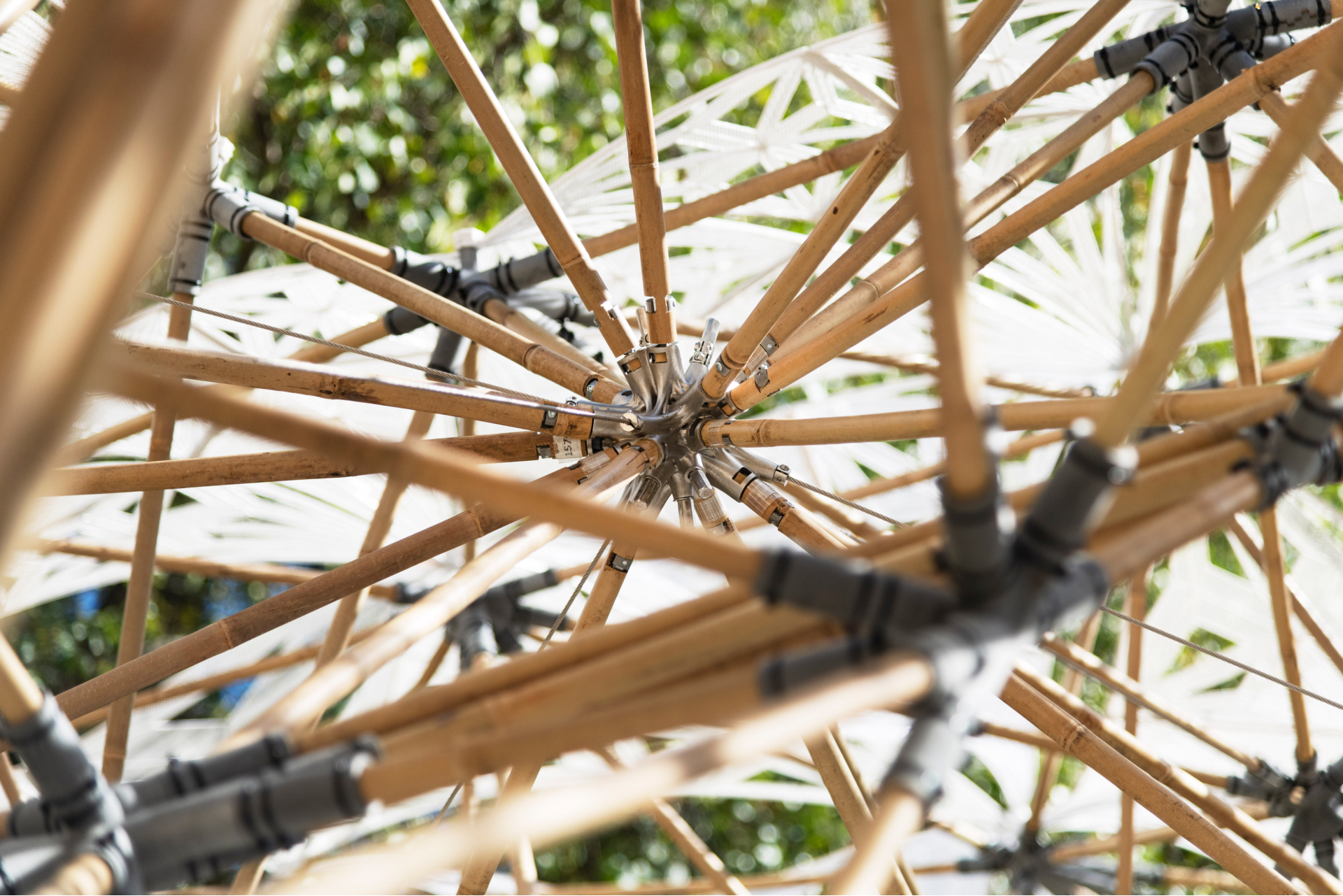
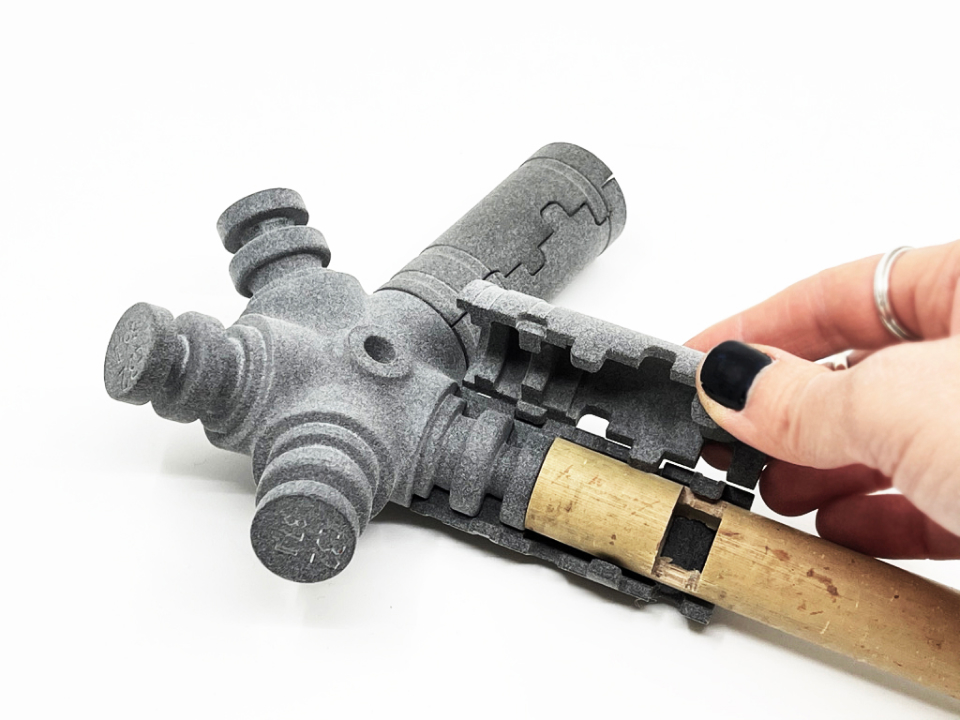